RMAs: Negative Experience or Valuable Opportunity?
June 29, 2018 | John Talbot, Tramonto CircuitsEstimated reading time: 1 minute
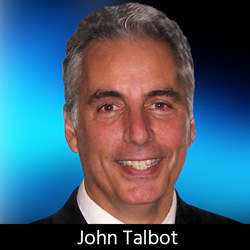
Returned product is inevitable if you work in manufacturing. That does not imply that it is easy to address. No matter what the reason for the returned material, it disrupts the normal flow of the quality and manufacturing teams. An inspector must first review the defect and agree that it is indeed a defect. This seems like a simple task and can be if the material doesn’t match a customer specific requirement.
However, if the material must adhere to an industry-wide standard, such as an IPC standard in the circuit industry, it becomes a little more tedious. In most cases the manufacturer will be more familiar with the specification than their customer. Also, they are more likely to keep the latest revision of the requirements in their library. This can cause a situation where the customer has identified a reject that isn’t agreed upon when compared to the standard it was built to. Tedious indeed!
As well, there are other cases that have been witnessed by the author that create a lessthan-easy situation. For instance, if the customer sends back rejected material that wasn’t built by your company. This is typically easy to determine by company markings. Or they send back materials that have obviously been damaged by handling at their own facility. It complicates an already difficult process.
How does it happen?
In the flexible circuit industry (and any other industry, for that matter), there are times when all the material delivered to the customer fails to meet the specifications. This can happen for a number of reasons and typically depends on the final inspection process. Two common final inspection processes used are sampling and 100%. When a product utilizes the 100% inspection process, every part that is shipped to your customer will also have been inspected. A sampling process is intuitively a partial inspection, typically 10-25% of the total, and is used on products that have a long history of zero defects.
To read the full version of this article which originally appeared in the April 2018 issue of Flex007 Magazine, click here.
Suggested Items
KIC’s Miles Moreau to Present Profiling Basics and Best Practices at SMTA Wisconsin Chapter PCBA Profile Workshop
01/25/2024 | KICKIC, a renowned pioneer in thermal process and temperature measurement solutions for electronics manufacturing, announces that Miles Moreau, General Manager, will be a featured speaker at the SMTA Wisconsin Chapter In-Person PCBA Profile Workshop.
The Drive Toward UHDI and Substrates
09/20/2023 | I-Connect007 Editorial TeamPanasonic’s Darren Hitchcock spoke with the I-Connect007 Editorial Team on the complexities of moving toward ultra HDI manufacturing. As we learn in this conversation, the number of shifting constraints relative to traditional PCB fabrication is quite large and can sometimes conflict with each other.
Standard Of Excellence: The Products of the Future
09/19/2023 | Anaya Vardya -- Column: Standard of ExcellenceIn my last column, I discussed cutting-edge innovations in printed circuit board technology, focusing on innovative trends in ultra HDI, embedded passives and components, green PCBs, and advanced substrate materials. This month, I’m following up with the products these new PCB technologies are destined for. Why do we need all these new technologies?
Experience ViTrox's State-of-the-Art Offerings at SMTA Guadalajara 2023 Presented by Sales Channel Partner—SMTo Engineering
09/18/2023 | ViTroxViTrox, which aims to be the world’s most trusted technology company, is excited to announce that our trusted Sales Channel Partner (SCP) in Mexico, SMTo Engineering, S.A. de C.V., will be participating in SMTA Guadalajara Expo & Tech Forum. They will be exhibiting in Booth #911 from the 25th to the 26th of October 2023, at the Expo Guadalajara in Jalisco, Mexico.
Intel Unveils Industry-Leading Glass Substrates to Meet Demand for More Powerful Compute
09/18/2023 | IntelIntel announced one of the industry’s first glass substrates for next-generation advanced packaging, planned for the latter part of this decade.